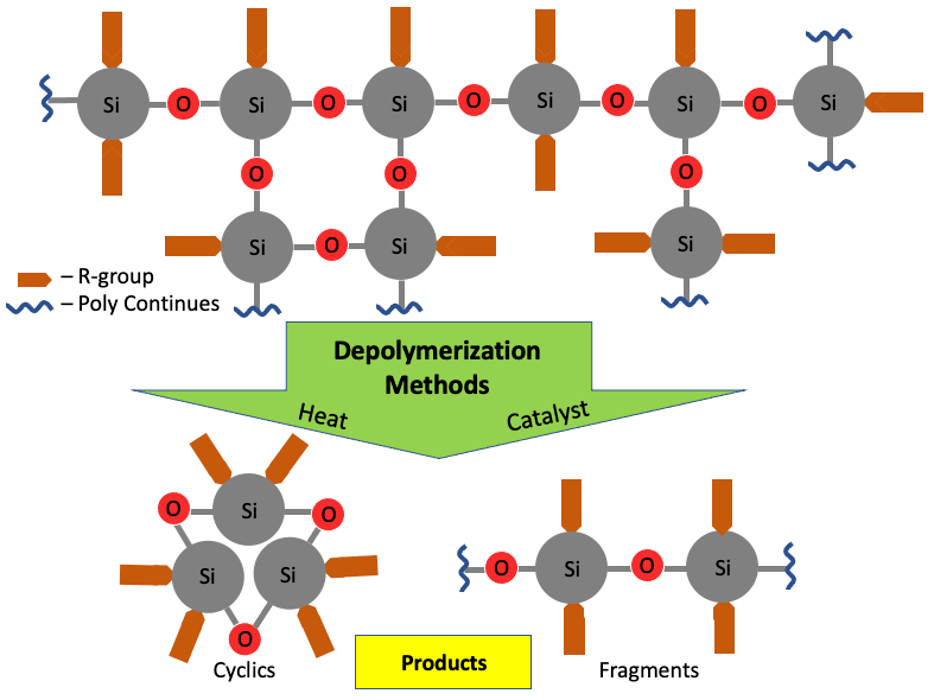
Closing the loop: BGSU researchers devise ‘green chemistry’ method to recycle, upcycle silicone
Dr. Joe Furgal’s lab has developed a method that breaks down silicone at room temperature, allowing it to be remade into new materials
By Nick Piotrowicz
Silicone and other siloxane-based polymers are in countless consumer products, but their popularity comes with a catch: Almost all of them are thrown into landfills after one use.
Pioneering research at Bowling Green State University, however, could help change that.
Dr. Joe Furgal, an associate professor in the BGSU Chemistry Department, is spearheading a research project studying the use of room-temperature depolymerization to recycle or upcycle silicone, thus keeping them out of landfills and saving massive amounts of energy required to create new polymers.
The life cycle of silicone has a clear gap, Furgal said. After consumer use, there currently is no easy way to turn the material back into its original form and be reused like other materials.
“After you use it, you just throw it away because silicones aren’t recycled,” he said. “There’s no recycling number for silicone, and there’s not even really a good process for it out there.”
Wide appeal
Medical applications account for significant amounts of silicone usage — in tubing, hearing aids, implantable devices and prosthetics — but silicone also has significant everyday usage in things like kitchen tools, pacifiers, baby bottles, caulking and even children’s toys such as Silly Putty.
Additionally, these polymers are used to make everything from gaskets to insulation for aerospace to the primary material to make cinematic masks in Hollywood.
But once they’re used for the initial purpose, there is not currently a practical or cost-effective method of reusing the material.
Dr. Kalani Edirisinghe, a postdoctoral research associate in Furgal’s lab, said that silicone and other similar polymers offer many benefits, but when these polymers are discarded, the process of replacing them means significant, new energy usage.
“Siloxane-based polymers are widely used in everyday materials because they are low toxicity, and they're chemically, mechanically and thermally stable,” Edirisinghe said. “The high energy cost in producing these materials is lost when they are discarded without recycling or upcycling, which will be a waste of resources and energy.”
Similar to steel production, the creation of siloxane-based polymers requires carbothermal reduction at temperatures higher than 3,600 degrees Fahrenheit.
Conservative estimates indicate every produced kilogram of the metal silicon, which is used to make the polymer silicone, releases at least 10 times that amount of carbon dioxide — and humans produce about 1.5 million tons of silicone per year.
“We wanted to make the silicone life cycle more like steel,” said Dr. Buddhima Rupasinghe '22, the author of a review on silicone degradation processes whose research as a BGSU student was responsible for moving this technology forward.
But silicone is unlike steel after it is used by consumers. Most post-consumer steel is collected and reused, and Furgal said he wanted to use this research to “close the loop,” by returning polymers to their original forms, allowing them to be reused.
“Our inspiration comes from steel, which is made by a very similar process to silicon — but steel has an 88% recycling rate,” he said. “Think about that: 88% of all steel is reused, and steel scrap uses about 75% less energy than new steel.”
Green chemistry
The process of turning silicones back into raw materials uses a process called depolymerization, which is the process of converting a polymer — with grouped subunits — back into a monomer or series of monomers that allows them to be reused.
The research, which included collaboration and a student exchange program with Central State University, studied how the reaction could take place at room temperature to depolymerize silicone.
Furgal’s lab uses a catalyst that breaks down the silicone’s bonds, a solvent to aid catalyst transfer into the silicone, followed by a calcium chloride bath to lock the new structure into place.
The resulting liquid can be strained and reused in new silicone production — eliminating the energy-heavy first step of silicone creation.
“We can take silicones, silicone rubbers, elastomers, oil, and using catalysts at room temperature, we can convert them back to their starting material,” Furgal said. “After filtering, then you can put that right back into the initiator process to get back to silicone.”
The depolymerization method even can separate silicone from attached plastics without harming the latter, and also can repurpose medical silicone, as the solvent also kills any biohazards the silicone might have encountered during its first use.
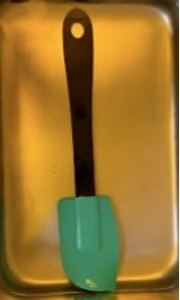
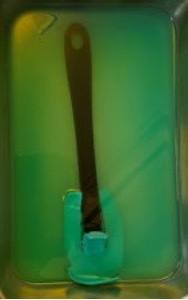
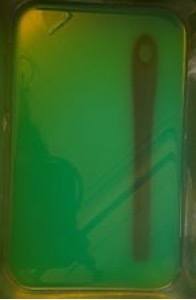
The patent-pending methodology has a promising future use that includes a grant from the National Heart, Lung, and Blood Institute to study the enhanced use of silicone with the controlled release of nitric oxide to prevent infection and blood clotting, a collaboration with associate professor Dr. Alexis Ostrowski at BGSU and two biomedical engineering faculty members at the University of Georgia, Dr. Elizabeth Brisbois and Dr. Hitesh Handa.
The researchers are hopeful these methods will be useful and wide-ranging in reducing carbon emissions caused by the initial creation of silicone and similar polymers.
“This research opens the possibility of depolymerizing these materials in mild conditions and at room temperature,” Edirisinghe said. “This process will save resources, energy and cost because it’s environmentally beneficial and will contribute to green chemistry and the sustainable use of resources.”
Related Stories
Media Contact | Michael Bratton | mbratto@bgsu.edu | 419-372-6349
Updated: 06/27/2023 10:39AM